Motor armatures are critical components in electric motors, serving as the central part of the motor's operation. Proper maintenance and regular checks of the motor armature are essential to ensure the efficiency and longevity of the motor. This article provides a detailed, professional, and technically robust guide on how to check a motor armature.
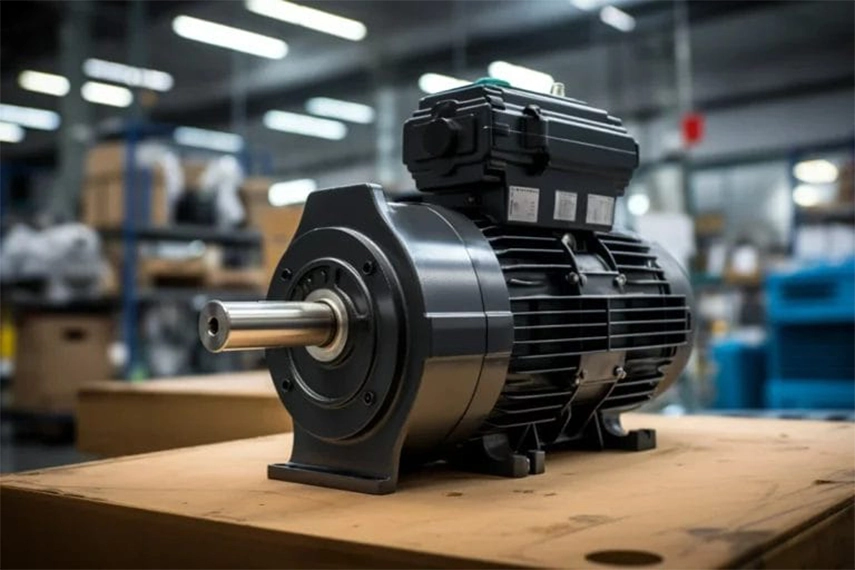
Understanding the Motor Armature
What is a Motor Armature?
The armature is a fundamental part of an electric motor, typically consisting of a shaft, winding, and commutator. The winding is the wire wrapped around the armature, creating an electromagnet when current flows through it. The commutator is a rotary switch that reverses the direction of current flow through the winding, facilitating continuous rotation.
Function of the Armature
The primary function of the armature is to interact with the magnetic field in the motor, producing torque that turns the motor shaft. It is crucial for converting electrical energy into mechanical energy. Any issues with the armature can significantly impact the motor's performance.
Steps to Check a Motor Armature
Visual Inspection
A thorough visual inspection is the first step in checking a motor armature. Look for obvious signs of damage or wear, such as burnt spots, broken wires, or loose connections.
Steps for Visual Inspection
- Remove the Armature: Carefully disassemble the motor to access the armature. Ensure the power is disconnected before starting.
- Inspect the Winding: Check for any visible signs of damage on the winding. Look for discoloration, which may indicate overheating.
- Examine the Commutator: The commutator should be clean and free of grooves. Excessive wear or scoring can affect motor performance.
- Check for Loose Connections: Ensure all connections are tight and secure. Loose connections can lead to poor performance and potential damage.
Electrical Testing
After a visual inspection, perform electrical tests to identify any internal issues that may not be visible.
Continuity Test
A continuity test checks if there is an unbroken electrical path within the winding.
- Set Up Multimeter: Set the multimeter to the continuity mode.
- Test the Winding: Place one probe on one end of the winding and the other probe on the opposite end. A continuous path will emit a beep or show a low resistance value on the multimeter.
- Check Multiple Points: Test at various points to ensure continuity throughout the winding.
Insulation Resistance Test
This test measures the resistance between the winding and the motor frame, indicating the quality of insulation.
- Set Up Insulation Tester: Use a megohmmeter or insulation resistance tester.
- Connect Probes: Connect one probe to the winding and the other to the motor frame.
- Measure Resistance: A high resistance value (typically in the megohms) indicates good insulation, while a low value suggests insulation failure.
Bar-to-Bar Test
This test checks the integrity of the commutator bars and the connections to the winding.
- Set Up Multimeter: Set the multimeter to the resistance mode.
- Test Adjacent Bars: Place the probes on two adjacent commutator bars.
- Compare Readings: The resistance should be consistent between all adjacent bars. Significant variations indicate a problem.
Mechanical Checks
Mechanical issues can also affect the performance of the armature. Ensure that the armature is free of mechanical defects.
Bearing Inspection
Bearings support the armature and allow it to rotate smoothly. Worn or damaged bearings can cause excessive vibration and noise.
- Inspect Bearings: Check for signs of wear, such as pitting or rough surfaces.
- Check for Play: Wiggle the armature to check for excessive play, which indicates worn bearings.
- Lubricate or Replace: Lubricate the bearings if they are in good condition. Replace them if they are worn or damaged.
Shaft Alignment
A misaligned shaft can cause uneven wear and mechanical failure.
- Check Alignment: Use a straightedge or alignment tool to check the alignment of the shaft.
- Correct Misalignment: Adjust the position of the motor or the mounting to correct any misalignment.
Functional Testing
After performing visual, electrical, and mechanical checks, conduct a functional test to ensure the armature operates correctly under load.
- Reassemble the Motor: Carefully reassemble the motor, ensuring all components are correctly aligned and secured.
- Connect Power: Reconnect the motor to the power supply.
- Run the Motor: Run the motor and observe its operation. Listen for unusual noises, check for excessive vibration, and monitor the temperature.
- Load Test: Apply a load to the motor and check its performance. Ensure it runs smoothly and delivers the required torque.
Common Issues and Troubleshooting
Overheating
Overheating can cause significant damage to the armature winding and insulation.
Symptoms
- Discoloration of the winding
- Burnt smell
- Excessive heat during operation
Causes
- Overloading the motor
- Poor ventilation
- Electrical faults
Solutions
- Reduce the load on the motor
- Improve ventilation and cooling
- Repair or replace damaged components
Commutator Wear
Excessive wear on the commutator can lead to poor electrical contact and performance issues.
Symptoms
- Grooves or scoring on the commutator
- Sparking or arcing
- Inconsistent motor operation
Causes
- Incorrect brush pressure
- Contaminants on the commutator
- Worn brushes
Solutions
- Adjust brush pressure
- Clean the commutator
- Replace worn brushes
Electrical Faults
Electrical faults can result from damaged winding or poor connections.
Symptoms
- Inconsistent resistance readings
- Short circuits
- Motor fails to start or runs erratically
Causes
- Broken or damaged winding
- Loose connections
- Insulation failure
Solutions
- Repair or replace damaged winding
- Tighten connections
- Improve insulation
Conclusion
Checking a motor armature involves a combination of visual inspections, electrical tests, and mechanical checks to ensure the motor operates efficiently and reliably. By thoroughly examining the armature, identifying potential issues, and addressing them promptly, you can extend the lifespan of the motor and prevent costly downtime. This comprehensive approach to armature inspection and maintenance ensures optimal motor performance and reliability in demanding environments.